We offer:
- Superior quality coatings:
- Gloss, dull, raised, glitter and other specialty coatings
- The right finishing touches to your project
Equipment
- 2 Sakurai Screen Coaters (28” x 40”)
UV Coating… All-in-One Package
Ensure your packaging has that high-quality finished look!
UV Coating can add value to a wide variety of packaging displays. Here are a few concepts you can bring to your customer:
- Combination Spot and Raised UV:
- Spot and raised UV coating add texture and visual distinctness to any product on which they are applied.
Why not combine these two solutions to create a more compelling package design? Spot and raised UV coating will showcase your company’s brand or logo in a package that is impossible to miss!
- Satin and Gloss for Contrast:
- By applying satin and gloss for visual contrast, you will naturally draw the consumer’s guide to your packaging.
Try applying satin and high-gloss UV coating to adjacent areas of your package. Satin UV’s low-key, flat appearance and gloss’ UV brilliant finish beautifully offset each other creating an eye-catching package that will have the product flying off the shelf!

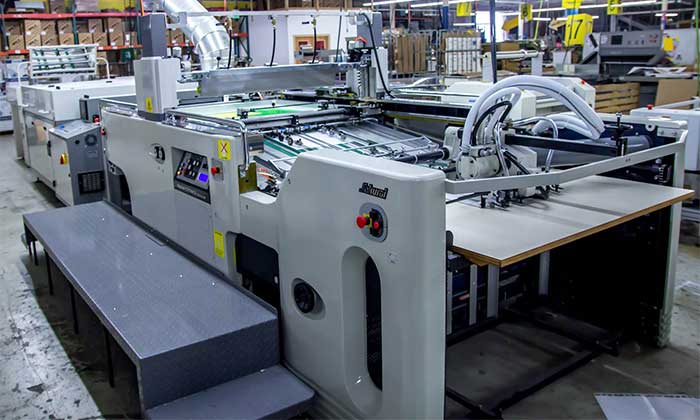
Tips for UV Coating Success
It is important to know how UV coating interacts with inks, stocks and adhesives. You can avoid many potential concerns prior to the start of production.
UV coating can only adhere to ink as effectively as the ink has bonded to the package. The UV coating is likely to scratch or scruff off if the ink on your package has not fully adhered to the package.
If you plan to apply a spot UV to a glued area, be sure to start with the glue first. UV coating should not be applied on areas to which a UPC code or other labels might be affixed.
Inks should be free of paraffin waxes, silicones or other slip additives. UV coatings do not adhere properly to these materials. Also, avoid inks with alkaline pigments, which are commonly found in Reflex blue, Rhodamine red, PMS purple, or any dark blue-to-violet color ink. Although these inks can normally be coated, they tend to bleed and can cause the coating’s color to change or be altered.
Let your inks dry completely. The inks on your printed package must be completely dry prior to the application of a UV coating. Normal drying times are 24 to 48 hours prior to UV coating being applied. If your inks are emulsified, additional drying time may be required to ensure the UV coating process is successful. If the job will be UV coated on two sides, an extra day should be scheduled between applications.
UV coating should be applied to a smooth stock with a clay- or enamel-coated surface. Uncoated stocks will cause the UV to dry up, yellow, and crack off.
Services
Questions?
If you need a quote or have any questions, call us at 818-773-9337.